Table of Contents
- Introduction
- Understanding Lithography: The Art and Science
- The Game Changer: How Lithography Transformed Publishing
- From Stone to Silicon: The Digital Evolution
- Why Lithography Still Matters in the Digital Age
- Embracing the Future: Innovations in Lithographic Technology
- Conclusion
Introduction
The write-up discusses how lithography transformed publishing. Lithography, which means “writing on stone” in Greek, is a printing process that was invented in 1796 by German author Alois Senefelder.
Senefelder discovered that oil and water do not mix, transferring images drawn with oil-based inks to a flat surface. This discovery marked a major shift from previous manual printing methods like woodblock printing or movable typesetting.
The Origins of Lithography in the Late 18th Century
Senefelder first developed lithography in the late 1700s as a low-cost way to self-publish his plays and sheet music. He eliminated the need for expensive copper engraving by using smooth stones as printing plates.
His technique involved using a grease pencil to draw an image onto a limestone block and then etching the stone with acid solutions to fix the drawing. The stone was inked, with water keeping the ink from sticking to the blank areas. Paper was then pressed against it to transfer the image.
The Shift from Manual Printing Methods
Lithography presented significant advantages over existing print methods. It was much faster than painstakingly hand-carving wooden blocks or setting movable type. The printing press allowed lithographs to be mass-produced more efficiently. Lithography also created finer, more detailed imprints. By the early 1800s, the process spread across Europe, and lithographic studios opened to meet rising demand.
The Publishing Revolution Sparked by Lithography
The introduction of lithography sparked a revolution in publishing. Printers could produce sharp, intricate illustrations affordably. Visual content gained immense popularity in newspapers, magazines, posters, packaging, and advertising.
Lithography even enabled high-quality art reproductions, bringing famous works to the public. This accessible printing process directly contributed to mass communication and the spread of information in the 19th century.
The stage is now set to explore precisely how lithography technically works and its tremendous impact on publishing and society in the following sections.
Understanding Lithography: The Art and Science
Lithography is based on the simple principle that oil and water do not mix. The process involves using an oil-based ink to draw an image onto the surface of a limestone plate. The stone is then moistened, and the water sticks to the surface while the oily ink repels it. When paper is pressed against the surface, the ink transfers to the paper while the water keeps the bare stone clean.
The Materials and Tools Behind the Magic
Traditional lithography requires only a few key materials and tools. The printing surface is usually high-quality limestone chosen for its fine grain and ability to absorb oil and water. Lithographers use special oil-based inks that contain wax, grease, or other oily substances to make the drawings. Using a brush or pen, the inks are applied with a lithography crayon or liquid ink.
Once the image is drawn, the stone is treated with solutions that etch the surface and make the image receptive to oil-based inks. A printing press applies pressure to transfer the inked image onto paper. The paper must have the right absorbency so the ink adheres properly.
Advancing a Classic Art Form Through Technology
While the basic principles remain the same, lithography has evolved enormously thanks to technological innovations. For example, the printing surface expanded from limestone to include metal plates, plastic sheets, and rubber blankets.
Photolithography uses photos to transfer images onto the printing surface instead of hand drawing. Computer-to-plate systems now translate digital files directly into etched metal plates ready for the printing press. These technologies increased efficiency, consistency, and design options compared to traditional hand-drawn methods.
Modern lithographic presses feature computerized ink and dampening control, integrated plate imaging, and automated paper handling. As a result, today’s lithographic prints can be created faster and more intricately than ever.
These innovations allowed lithography to remain a preferred printing technique, even with the rise of digital publishing. The classical art form endures by embracing science and technology without sacrificing the foundational principles established over 200 years ago.
The Game Changer: How Lithography Transformed Publishing
Before the advent of lithography in the late 18th century, publishers relied on labor-intensive printing methods like woodblock printing and movable typesetting. These techniques severely limited the length of print runs and the complexity of page layouts. As demand grew for more affordable books and printed images, the tedious process of carving woodblocks or setting type by hand became a major bottleneck.
With woodblock printing, a block had to be carved by hand for every page. Making changes was incredibly difficult. Typesetting with movable metal letters was faster than woodblocks but required manually placing each letter. Publishers struggled to keep up with the public’s growing appetite for printed materials using these conventional methods.
Lithography provided a revolutionary alternative. By exploiting the chemical principle that oil and water repel, lithographic stones could be used to mass-produce prints and books. The process allowed publishers to:
- Speed up book printing with high-volume lithographic presses
- Achieve finer details than woodblocks permitted
- Print subtle tonal gradations impossible with metal-type
- Reuse lithographic stones, reducing costs
- Print intricate images seamlessly with the text
With lithography dramatically accelerating printing, publishers could release books, magazines, newspapers, and artwork reproductions on a much larger scale than before.
Lithography was pivotal in transforming publishing by permitting innovations like:
- Penny presses – Newspapers with wider circulation due to lower lithographic printing expenses
- Mass market paperbacks – Inexpensive books printed lithographically on low-cost paper
- Fine art reproductions – High-quality lithographic copies that popularized famous works
By enabling publishers to print faster, cheaper, and with better quality, lithography drove a boom in access to the printed word that shaped modern society.
From Stone to Silicon: The Digital Evolution
The transition from traditional analog lithography to digital printing technologies began in the 1970s with the invention of laser printers. These printers utilized lasers to etch images onto aluminum printing plates, replacing the hand-drawn plates used in lithography for over a century.
The Rise of Digital Printing
As computing advanced in the 1980s and 1990s, more aspects of the lithographic process shifted to the digital realm. Imagesetting allowed publishers to lay out pages on computers rather than manually, while computer-to-plate (CTP) technology enabled printing plates to be imaged directly from digital files. This increased efficiency reduced costs, and enabled more flexibility with design changes.
By 2000, most offset lithographic printing relied heavily on digital technology while retaining the high print quality associated with lithography. Digital solutions also paved the way for other significant innovations in printing, like print-on-demand and variable data printing. This gives more weightage to how lithography transformed publishing.
Implications for Publishing
The shift to digital brought seismic changes for publishers of all types:
- Shorter print runs became economically feasible, reducing waste
- Mass customization of documents for targeted audiences
- Faster turnaround times measured in hours rather than days
- On-demand printing enabled anyone to self-publish affordably
Overall, digital technology provides the flexibility and efficiency needed for publishers to thrive in an increasingly online world.
Environmental and Economic Benefits
Digitization made printing and publishing a greener industry. Reduced setup times cut waste from discarded press sheets, while digital files eliminated resource usage for steps like photographic processing. The precision of digital imaging also reduced misprints.
Digital printing similarly yields economic advantages. Lower costs for short-run and print-on-demand jobs enable niche offerings to be profitable. The technology also created market segments like customized marketing literature and user-generated content publishing.
By retaining the quality of lithography while gaining the flexibility of computers, digital printing delivers environmental and financial benefits compared to traditional techniques.
Why Lithography Still Matters in the Digital Age
Even in today’s digital world, lithographic principles play an important role in printing and publishing. Though offset lithography has largely been replaced by digital solutions, traditional lithographic techniques offer unparalleled quality and artistry that keeps them relevant for certain applications.
Enduring Relevance of Lithographic Principles
At its core, lithography is based on the principle that oil and water do not mix. This allows areas treated with oil-based inks to repel water and vice versa effectively. The same principle is leveraged in modern offset printing presses and platemaking to control ink application and produce crisp, vibrant images.
Digital printing uses different techniques, but understanding lithographic principles helps in areas like color separation, image processing, and quality control. Concepts of resolution, dot gain, and color rendering have their roots in lithography.
Preference for Niche Applications
For general use, digital printing beats lithography hands down in cost, speed, and flexibility. However, lithography still reigns supreme when it comes to producing:
- Fine art prints and reproductions
- High-end packaging like perfume boxes
- Postage stamps, banknotes, securities
- Metal cans, decals, and labels
The depth and subtlety of color possible with lithographed prints are hard to match digitally. The technique also allows printing on non-paper surfaces like metal sheets.
Preserving Printing Heritage
Handmade lithographic prints connect us to the rich history of printing and human creative expression. Though cumbersome, traditional lithographic methods embody unquantifiable cultural value.
Techniques like stone lithography preserve historical printing knowledge and let art students connect more intimately with the printmaking tradition.
As carriers of heritage, many lithographic presses have been preserved in museums. Exhibiting this equipment helps the public understand and appreciate books and artworks from centuries past.
Embracing the Future: Innovations in Lithographic Technology
Lithography continues to evolve with exciting innovations pushing printing technology’s boundaries. One area seeing rapid advancement is nanolithography, which uses nanoscale patterning techniques to create tiny, precise, integrated circuit patterns.
Nanolithography and Electronics
Nanolithography allows the production of transistors, memory chips, and processors that are more powerful, energy-efficient, and compact than ever before. Techniques like extreme ultraviolet lithography (EUV) and electron beam lithography (EBL) enable chipmakers to pack over a billion transistors into an area the size of a fingernail.
As nanolithography matures, it could revolutionize fields like microelectronics, telecommunications, computing, and more. The future possibilities are thrilling.
Hybrid Digital and Analog Solutions
Savvy publishers also embrace the best of both worlds by combining traditional lithographic printing with digital distribution and print-on-demand. This allows the superior print quality and aesthetic appeal of lithography for small batches and special editions, complemented by the convenience and customization of digital printing.
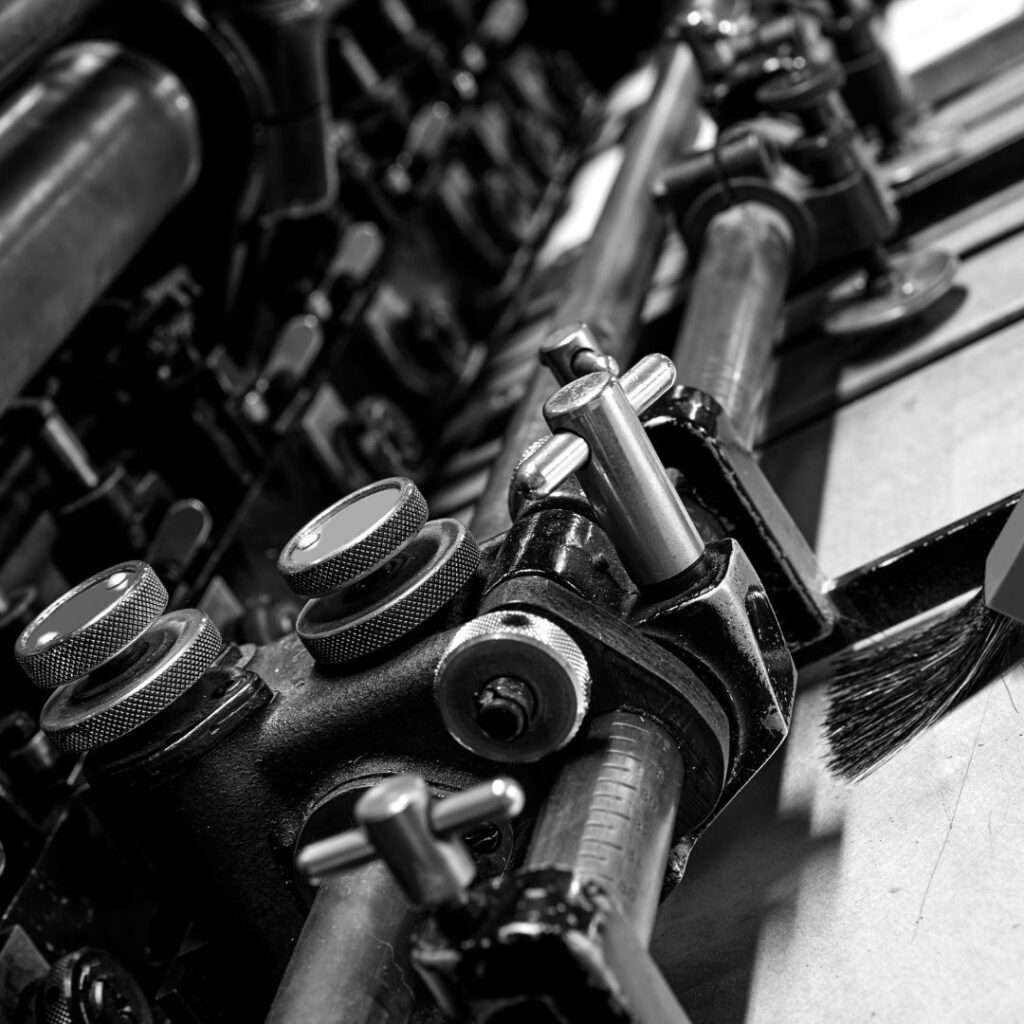
Some publishers even use digital storefronts and platforms to take orders and then produce requested prints using lithographic presses. This innovative hybrid model gives customers the benefits of analog quality and digital flexibility.
The Future of Publishing
As nanolithography and other advances make printing even more sophisticated and accessible, publishers can experiment with formats like interactive hybrid books, AR pop-up books, customizable manuscripts, and more.
Lithography will continue opening creative possibilities for publishers to engage and excite readers. The interplay between traditional techniques and emerging technologies promises a bright, vibrant future for the publishing landscape.
Conclusion
We have explored an interesting story of how lithography transformed publishing. Lithography has had a revolutionary impact on publishing over the past few centuries. From its origins in late 18th century Germany to today’s digital innovations, lithographic principles have enabled the mass production of printed materials at ever-greater speeds.
By allowing intricate images and textures to be reproduced on flat surfaces, lithography made high-quality color printing financially viable for books, newspapers, packaging, and more.
The transition from slow, manual printing presses to automated lithography machines marked a seismic shift for publishers. Runs that would have taken weeks could now be completed in days. This drove down costs and prices, bringing printed materials into the hands of more people than ever before. Further innovations like offset printing and digital lithography have only accelerated this trend.
Appreciate the Printing Process
When you read a crisp, vibrantly colored book or examine the fine details on a product package, consider the technical mastery required to produce it. Modern publishers stand on the shoulders of generations of lithographers, engineers, and designers who found ways to translate images and text reliably onto paper.
Appreciating the hidden craft behind the printed world can rekindle our sense of wonder. The next time you turn the pages of a book, take a moment to admire the depth and clarity of its printing.